A Closed-Loop Bin Picking System for Entangled Wire Harnesses using Bimanual and Dynamic Manipulation
Xinyi Zhang1, Yukiyasu Domae2, Weiwei Wan1, Kensuke Harada1,2
1Osaka University, 2National Institute of Advanced Industrial Science and Technology (AIST)
This paper addresses the challenge of industrial bin picking using entangled wire harnesses. Wire harnesses are essential in manufacturing but poses challenges in automation due to their complex geometries and propensity for entanglement. Our previous work tackled this issue by proposing a quasi-static pulling motion to separate the entangled wire harnesses. However, it still lacks sufficiency and generalization to various shapes and structures. In this paper, we deploy a dual-arm robot that can grasp, extract and disentangle wire harnesses from dense clutter using dynamic manipulation. The robot can swing to dynamically discard the entangled objects and regrasp to adjust the undesirable grasp pose. To improve the robustness and accuracy of the system, we leverage a closed-loop framework that uses haptic feedback to detect entanglement in real-time and flexibly adjust system parameters. Our bin picking system achieves an overall success rate of 91.2% in the real-world experiments using two different types of long wire harnesses. It demonstrates the effectiveness of our system in handling various wire harnesses for industrial bin picking.
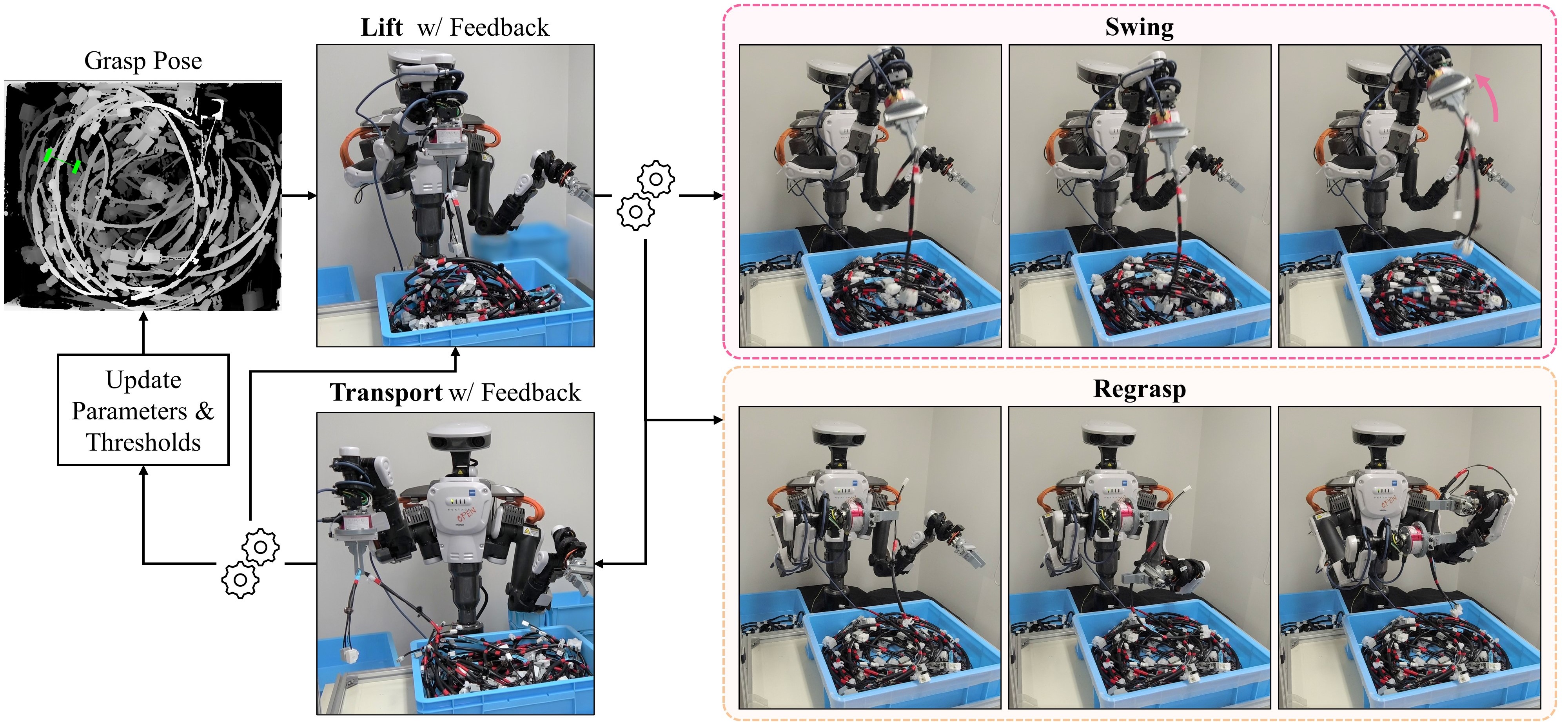
Supplementary Video
Demo
Picking atttempts using two types of wire harnesses.
Detect entanglement and swing
Detect entanglemenet and regrasp
Swing and regrasp
Swing for the longer object
Initial swing fails, increase swing angles
Swing and regrasp for the longer object
Slow motion for swing
We implement the swing motion using three joint angles of the right arm of the robot.
Video for regrasping motion
Rergrasping is perform only with the assistance of haptic.
Force output for predicting the subsequent actions
We use force feedback to determine the actions of transporting, regrasping, swing. If the force exceeds the threshold, the robot immediately stop the current movement and perform disentangling motions. The threshold can be adjusted during picking.
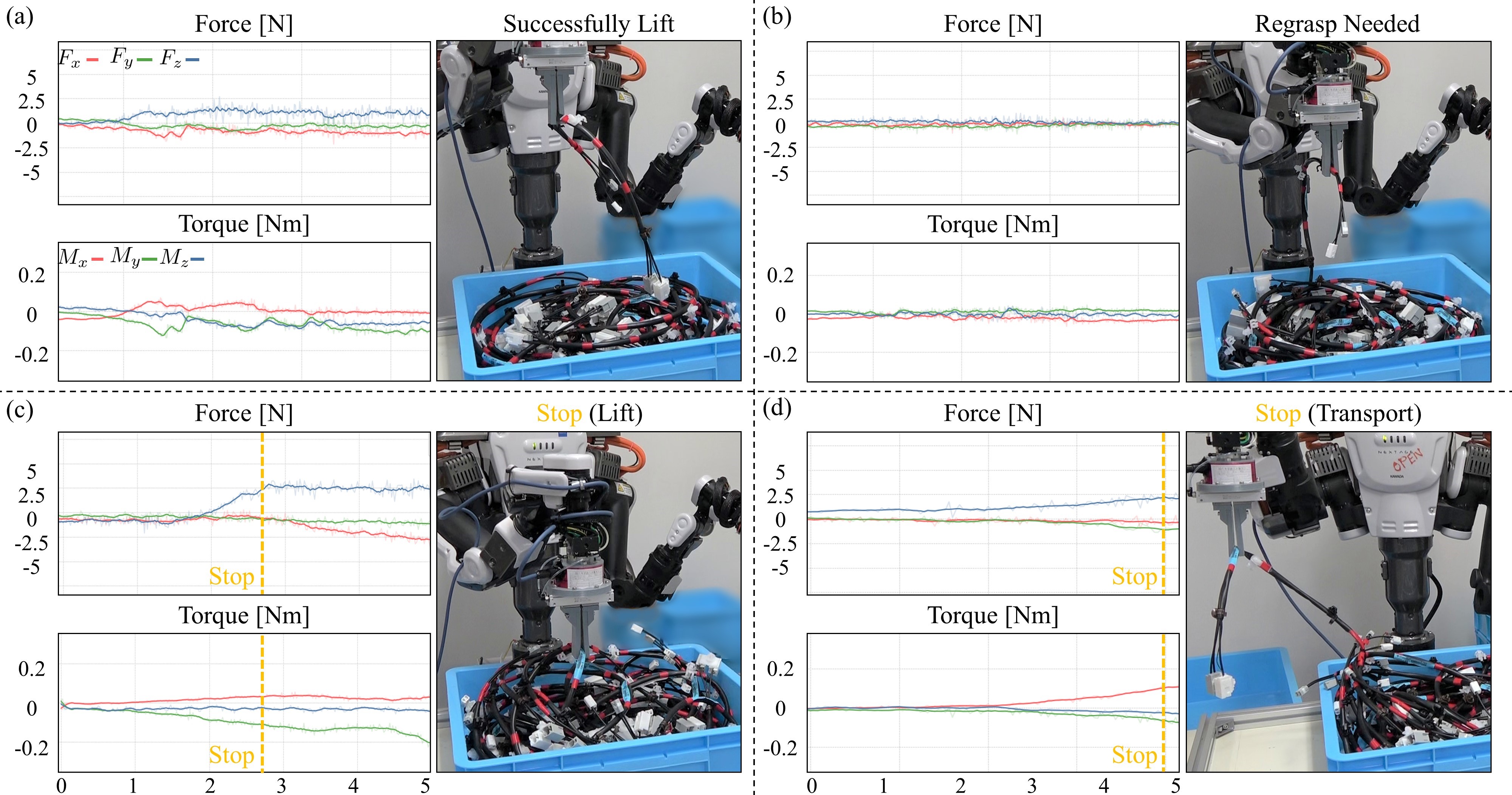
Acknowledgements
This work is supported by Toyota Motor Coorporation.